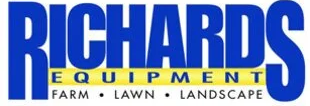
NUMBER OF ROWS 12 ROW WIDTH (IN. (MM)) 30 (762) | |
EFFICIENT HARVESTING IN DOWN CROPSThe front profile has been redesigned to expose the gathering chains. This is ideal when working in down corn, as the stalks are actively fed into the header to ensure that all cobs are collected, as well as speeding up harvesting. | |
MODERN CORN HEADERS FOR MODERN CORN FARMINGThe shorter points better follow ground contours to prevent "run-down" of valuable crops. The gills direct any loose kernels to the rear of the header, consigning lost cobs to the history books. | |
DEPENDABLE OPERATIONNew Holland corn headers are designed for top harvesting performance in all crop conditions. The stalk rolls have four knives to aggressively pull down stalks of any size, and the deck plates are electronically adjustable from the cab to adapt to changing stalk and cob size. | |
FLIP-UP OR RIGID: THE CHOICE IS YOURSRigid headers are available in 6-, 8-, 12- and 16-row configurations to enable you to choose just the right size for your fields. Both the rigid and folding versions deliver improved harvesting productivity and reliability. |
THE NEXT GENERATION OF CORN HEADERSNew Holland knows that it is the small things that can make an enormous difference when it comes to efficient harvesting. That is why a 360° vision of corn header development was taken into account when designing the new header. Extensive testing was carried out in Europe, North America and South America to ensure that the new generation of corn headers is right for your farm. |
FLEXIBLE, DURABLE POINTS
The islands and dividers are produced using advanced rotomolding techniques and are exclusively constructed of plastic. This means that they can, literally, take a battering and bounce back to their previous shape. In addition, their polyethylene construction absorbs impact, so the ears don’t bounce out of the corn header. The result: lower losses and higher capacity. This is perfect when working in the harshest conditions, as you’ll save both time and money. |
REDESIGNED FENDERS ENHANCE PRODUCTIVITY
The header fenders have been completely redesigned to improve your profitability. We moved the powered auger divider to the outside of the fender which reduces ear loss in standing corn. Why? The cornstalks are safely gathered into the header and do not fall over the edge. Even if you’re not using the powered divider, the concave shape of the fender catches any falling ears and transfers them into the header for processing. |
FOLD UP POINTS FOR EASIER SERVICING
All points fold up simply and easily to enable easy access for routine checks, servicing and even cleaning. The dividers and fenders fold up on gas struts, halving the effort and facilitating access. They are even safer too, since a safety latch has been included in their design to keep them securely in position. |
PRECISION POINT ADJUSTMENTTwo built-in divider point adjustment settings have been developed to ensure your corn header always works at the most efficient setting for you. The rugged lynchpin enables overall point adjustment and this can be further fine-tuned by altering the bolt to help you achieve specific cutting heights. |
EVEN SAFER ROAD TRANSPORT
Safety is of prime concern when undertaking high-speed road transport. New latches securely hold the points in a vertical position to prevent dangerous dropdown. These latches have been extensively tested on the world’s bumpiest roads. |
SUNFLOWER AND TALL CORN KITSSpecialist sunflower growers can modify their existing corn headers with the addition of a sunflower harvesting attachment. The ‘‘V’’-shaped knife efficiently cuts the stem and swiftly transfers the head into the combine. New Holland has also developed a specific attachment for operations that work in extra-tall corn. Vertical fender extension plates prevent the loss of valuable cobs over the sides. |
CORNROWER SYSTEM: UNIFORM ONE-PASS SWATHING OF CORN STOVERThe integrated cornrower system for New Holland corn headers funnels the processed cornstalks into a bank of knives which deliver a super-fine chop of all stalks. This material is then directed into uniformly dense windrows for subsequent baling. Swaths are free from dirt and stones and also contain any lost kernels. The result: a quicker drying stover and up to 15% denser bales, which have higher nutritional and combustion profiles. The system can also be deactivated when traditional spreading is desired. |
Number of rows |
12 |
Row width (in. (mm)) |
30 (762) |
Remotely adjusted deck-plates |
Standard |
Integrated stalk choppers |
Optional |
Rotary dividers |
Optional |
Grooved dividers |
Standard |
Feeding auger diameter (in. (mm)) |
26 (660.4) |
Autofloat™ system |
Optional |
Weight, non-chopping (lbs. (kg)) |
9,686 (4393) |